Nomenclature :
- Vieille manette de jeu avec des petits joysticks analogiques sur lesquels on peut se repiquer avec le potentiomètre du palonnier (j’ai utilisé une Thrustmaster DualAnalog 4 de récup)
- Pignon et couvercle potentiomètre imprimés en résine (fichier FreeCad ici, fichiers STL pignon ici et couvercle ici). Attention il faudrait mettre du jeu en plus dans le pas de vis, car j’ai dû les reprendre à la lime pour que ça se visse.
- Potentiomètre 10Kohms dont la roue peut s’accrocher sur un axe de diamètre 3,2mm (j’ai récupéré le mien dans un oscilloscope destiné à la casse)
- 2 roulements de roue de tondeuse universels diamètre intérieur 10mm, + tige filetée M10 et écrous
Ci dessous le montage du pignon avec un roulement de chaque coté. Pour qu’il n’y ait pas de jeu, les roulements sont légèrement préchargés en serrant les deux écrous. Ces écrous sont bloqué au frein filet.

Le couvercle est vissé par dessus et encapsule l’écrou, une tige métallique est sertie dans le couvercle. Dans mon cas c’est une tige diamètre 3,2mm issue d’une électrode enrobée de soudage, débarrassée de son enrobage :
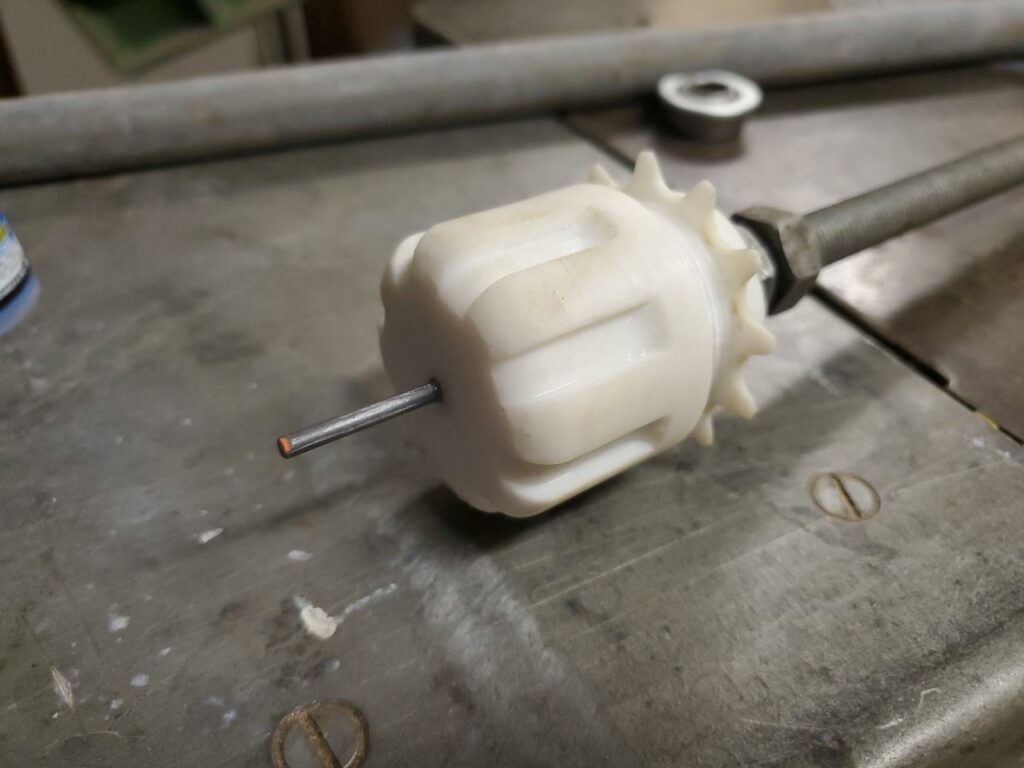
Montage d’essai avec la chaîne de vélo et le potentiomètre fixé en bout de la tige. Le potentiomètre tient par serrage sur la tige avec une vis pointeau. La carte électronique provient de la manette de jeu cannibalisée :
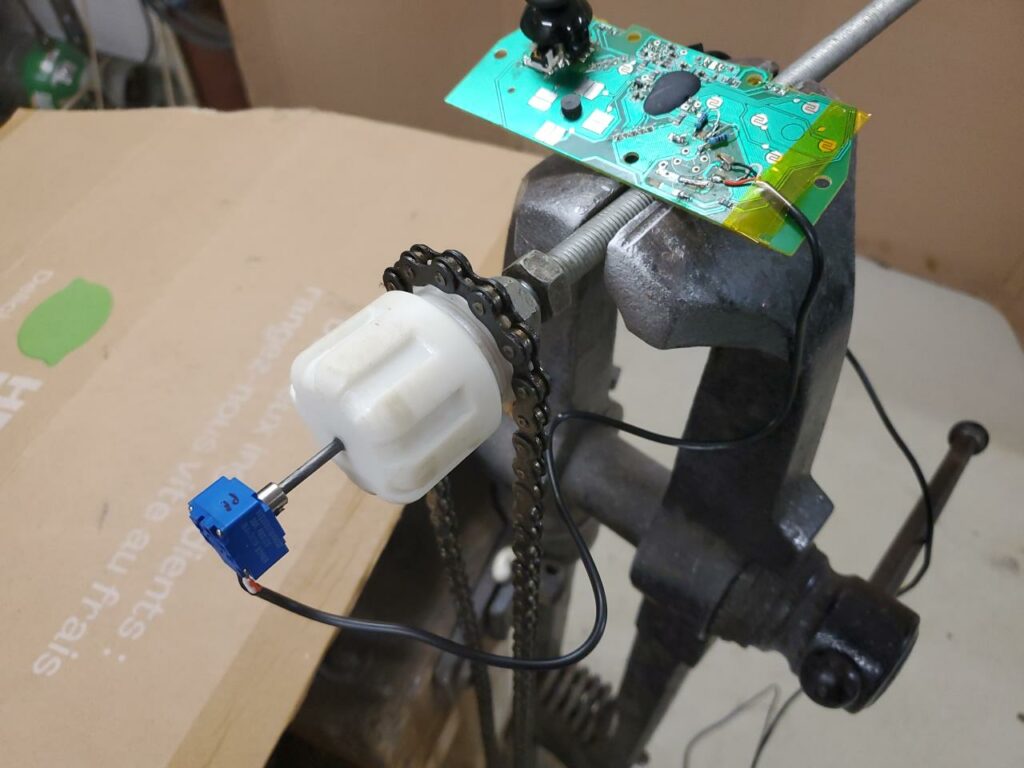
Construction du palonnier en bois, les dimensions sont sur mesure à mes pieds 🙂 Les pédales pivotent simplement grâce à une charnière fixée en dessous. Le pignon denté est maintenu par un fer en T adapté pour pencher le pignon au même angle que les pédales.
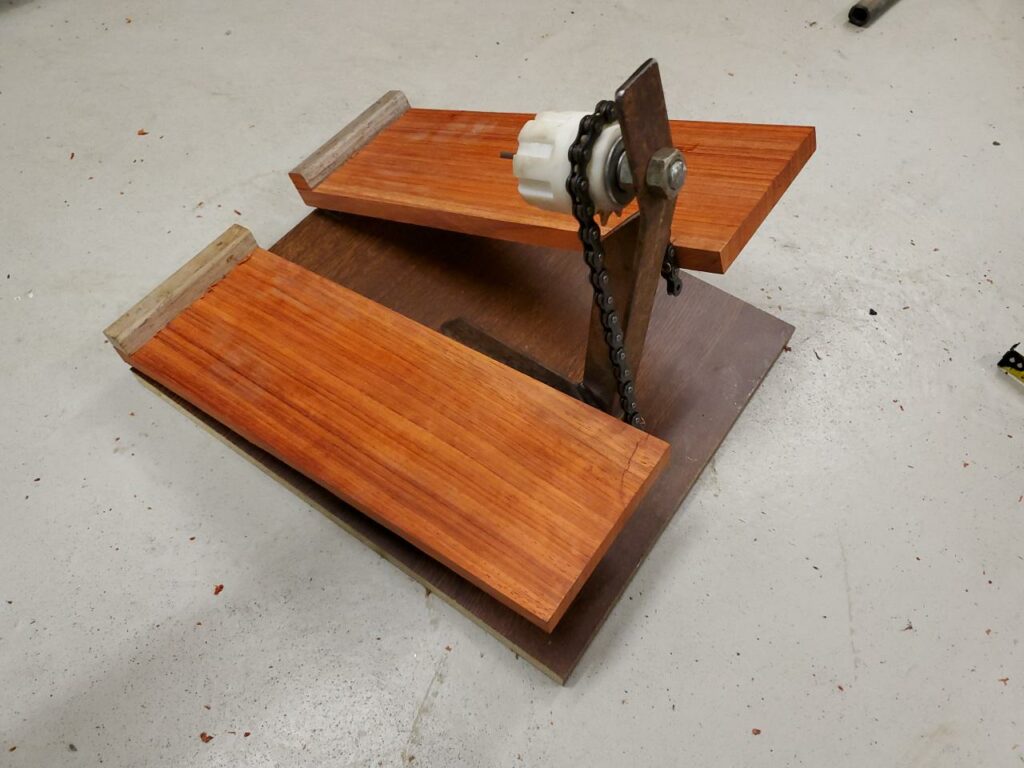
L’avantage de disposer le pignon au dessus du palonnier et d’utiliser une chaîne est que ça rentre très solide le palonnier, on se se mettre debout dessus sans souci…
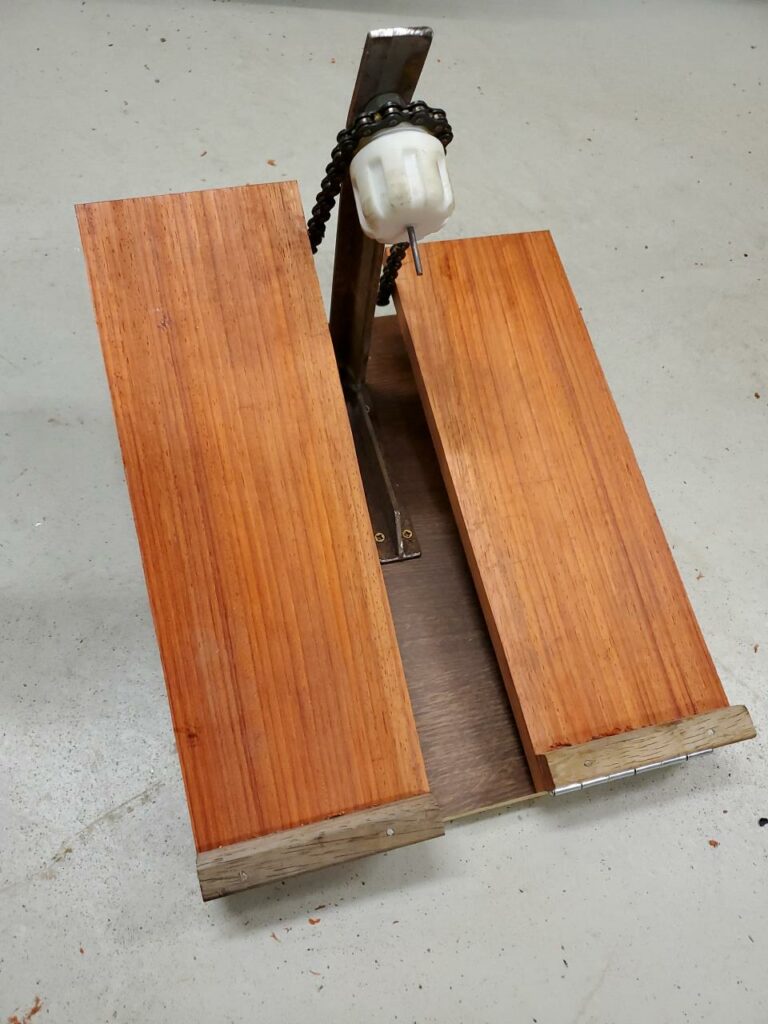
Détail de la fixation de la chaîne sur les pédales, vissée dans l’épaisseur, ce qui lui donne un degré de rotation. C’est nécessaire car ces points d’attache décrivent un arc de cercle alors que le pignon qui retient la chaîne ne peut tirer que dans une direction. Il faut donc qu’il y ait un peu de liberté pour « moyenner » le mouvement.
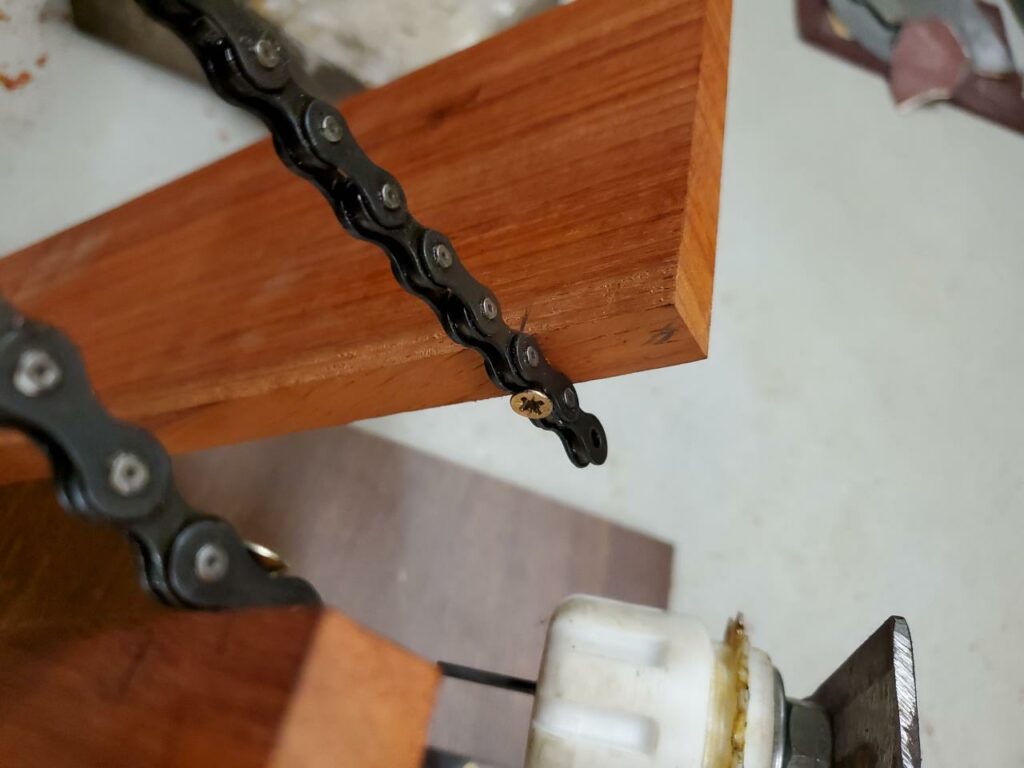
Ci dessous vue finalisée et fonctionnelle, les points supplémentaires sont :
- Des cales ont été collées sous les pédale pour limiter leur course vers le bas, ainsi on a un débattement de chaque pédale de +/-5cm. Avec le nombre de dents du pignon, cela provoque une rotation de 3/4 de tour du potentiomètre, qui correspond à sa course intrinsèque, et permet de ne pas le forcer en butée.
- Deux élastiques de rappel ont été fabriqués à partir d’un sandow, cela rend l’usage plus réaliste, et permet de remettre le palonnier automatiquement au neutre pour qu’il s’initialise sans offset quand on démarre le PC
- Le potentiomètre demande simplement a être bloqué en rotation (ici par une baguette collée dessus et coincée sur le fer en T), puisqu’il est fixé sur la tige du pignon.
- Le palonnier a été réhaussé pour être agréable a utiliser en position semi allongé (j’utilise un siège ikea comme fauteuil, assez représentatif de la position de pilotage)
- Le palonnier est fixé par des cordes au fauteuil, ce qui permet de bien s’appuyer dessus dans qu’il recule
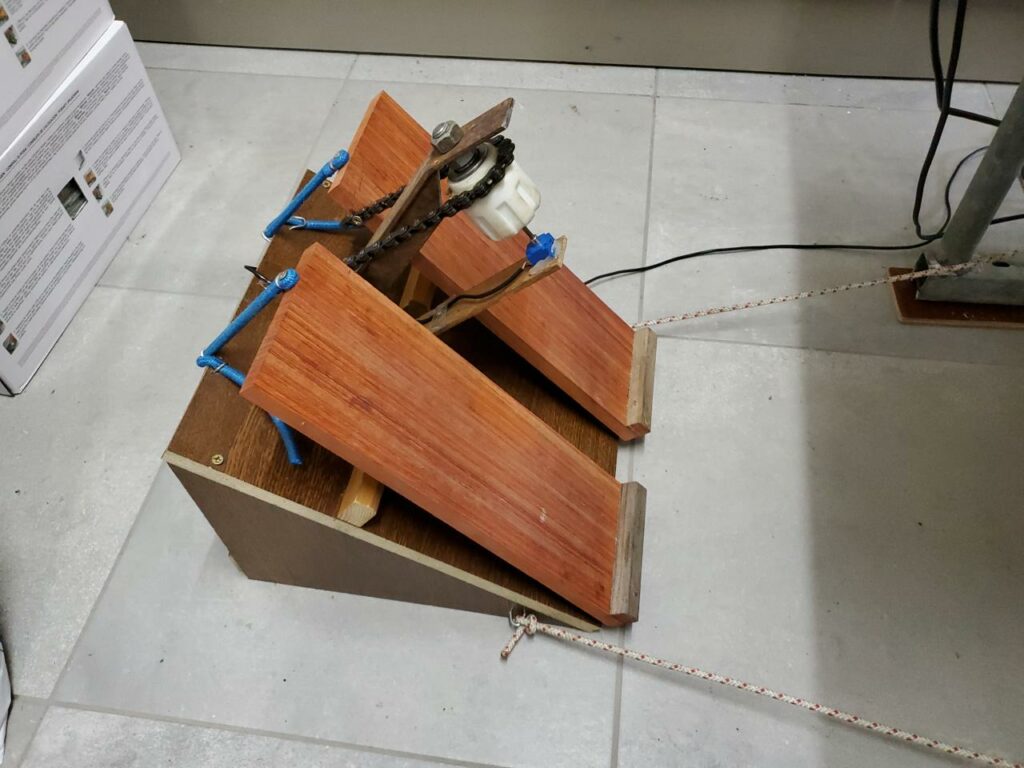